Композитные материалы в производстве защит картера двигателя.
Защиты картера и КПП из композитных материалов - это новейший, качественно усовершенствованный уровень защиты агрегатов и узлов двигателя вашего автомобиля.
Композитные защиты самые прочные (выдерживают поперечную нагрузку в 1,5-2,5 раза больше, чем сталь), а также самые легкие (в 3 раза легче стали). Технология изготовления таких защит позволяет придавать им сложные формы, в результате чего защита плотно прилегает к подрамнику автомобиля, максимально закрывает моторный отсек со всеми необходимыми изгибами и ребрами жесткости, защищает детали от грязи и не уменьшает клиренс. Композитные защиты не подвержены коррозии и окислению. Обеспечивают высокое шумопоглощение (для сравнения, при движении по гравийной дороге со стальной защитой возникает "шум пустого ведра", когда камушки стучат по листу металла). Композитные материалы не меняют своих свойств под воздействием влаги и атмосферных перепадов температур.
Композитный материал представляет собой искусственно созданный неоднородный сплошной материал, состоящий из двух или более компонентов с чёткой границей раздела между ними. Компоненты в свою очередь делятся на матрицу (или связующее) и включённые в неё армирующие элементы (или наполнители), которые обеспечивают необходимые механические характеристики материала (прочность, жёсткость и т. д.), а матрица обеспечивает совместную работу армирующих элементов и защиту их от механических повреждений и агрессивной химической среды. По типу наполнителей композиты для автозащит делятся на:
• стеклопластиковые (стеклоткань имеет белые волокна)
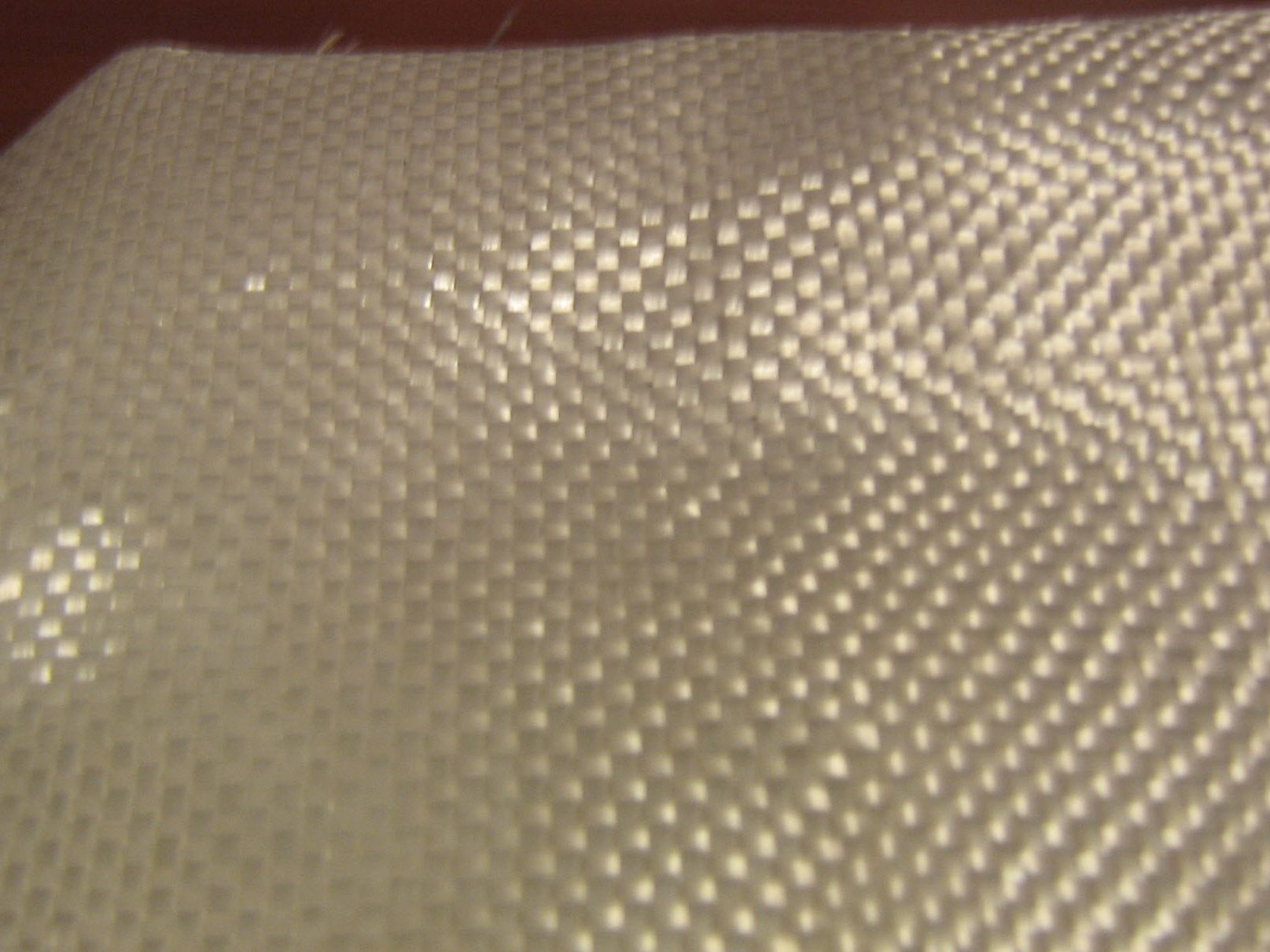
• кевларовые (волокна имеют зеленовато-золотистый цвет)
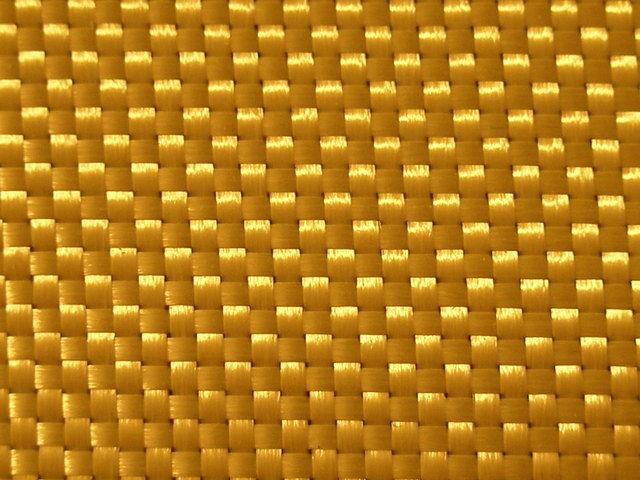
• карбоновые (или углепластиковые) (черные волокна)
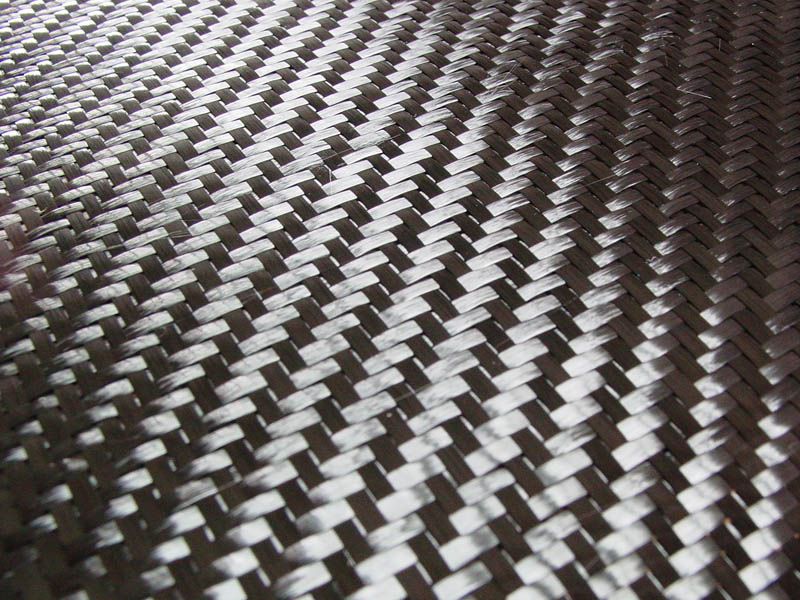
• базальтопластиковые (серые волокна)
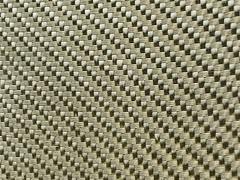
Самые популярные защиты из стеклопластика, прежде всего из-за оптимального соотношения "свойства/стоимость". Здесь качество изделия сильно зависит от вида стекловолокна, который использует производитель. Идеально, когда в качестве армирующего элемента используется стеклоткань, выкладываемая вручную. Но чаще вместо ткани берется ровинг (рубленное стекловолокно), которое вместе со смолой распыляется в форму. При этом частицы ровинга не переплетены друг с другом и связываются только смолой, для достижения нужной прочности приходится увеличивать толщину изделия. Защиты из стеклопластика обладают низкой теплопроводностью, влагостойки, светопроницаемы, устойчивы к механическим ударам и повреждениям, они не ржавеют, не теряют форму и не подвергаются тепловому воздействию.
Защиты из кевлара - самые дорогие. В основе материала - пара-арамидные (полипарафенилен-рефталамид) волокна, очень прочные и легкие. Изначально материал разрабатывался для армирования автомобильных шин, для чего он используется и теперь. Но благодаря своим уникальным свойствам стал широко применятся для изготовления средств индивидуальной защиты, например, защитные вставки в одежду для мотоспорта, антипрокольные стельки и, конечно, бронежилеты. Кевларовый композит прочнее стали в 2,5 раза и лучше стеклопластикового амортизирует ударные нагрузки. Это лучший материал для защит днища автомобиля.
Защиты из карбона (углепластика). Основная составляющая часть углепластика — очень тонкие нити углерода, сломать их очень просто, а вот порвать достаточно трудно. Из этих нитей сплетаются ткани с различным рисунком плетения (ёлочка, рогожа и др.). Для придания ещё большей прочности ткани из нитей углерода кладут слоями, каждый раз меняя угол направления плетения, детали будут жесткими там, где это необходимо, или гибкими — гасить вибрации, если это требуется. Слои скрепляются с помощью эпоксидных смол. Нити углерода получают термической обработкой химических или природных органических волокон, при которой в материале волокна остаются главным образом атомы углерода. Помимо обычных органических волокон (чаще всего вискозных и полиакрилонитрильных), для получения нитей углерода могут быть использованы специальные волокна из фенольных смол, лигнина, каменноугольных и нефтяных пеков. Кроме того, детали из карбона превосходят по прочности детали из стекловолокна, но, при этом, обходятся значительно дороже. Дороговизна карбона вызвана, прежде всего, более сложной, энергоемкой технологией производства и большей стоимостью производных материалов. Например, для проклейки слоев используются более дорогие и качественные смолы, чем при работе со стеклонитью, а для производства деталей требуется более дорогое оборудование (к примеру, такое как автоклав). Карбон не только легкий и прочный, но и очень жесткий материал. В этой жесткости кроется основной недостаток защит картера из углепластика - хрупкость, низкая стойкость по отношению к ударным нагрузкам. Также при производстве углепластиков необходимо очень строго выдерживать технологические параметры, при нарушении которых прочностные свойства изделий резко снижаются.
Защиты из базальтопластика. Этот материал - конкурент стеклопластика. По основным показателям - прочность, жесткость, стойкость к агрессивным средам, теплостойкость - базальтопластики превосходят стеклопластики на основе волокон из простого безщелочного стекла. Базальтовое волокно — материал, получаемый из природных минералов путём их расплавления и последующего преобразования в волокно без использования химических добавок. Базальт, из которого делают волокна, - это органический материал, в природе имеется в неограниченном количестве. Производство пластиков из базальтового волокна - сравнительно новая технология. В 2009 году немецкое инженерное бюро EDAG разработало концепт автомобиля, при производстве которого использовано базальтовое волокно. Как сообщается, «материал отличает лёгкость, прочность и экологичность, к тому же в производстве он обойдётся дешевле алюминия или углепластика».
Композитные защиты самые прочные (выдерживают поперечную нагрузку в 1,5-2,5 раза больше, чем сталь), а также самые легкие (в 3 раза легче стали). Технология изготовления таких защит позволяет придавать им сложные формы, в результате чего защита плотно прилегает к подрамнику автомобиля, максимально закрывает моторный отсек со всеми необходимыми изгибами и ребрами жесткости, защищает детали от грязи и не уменьшает клиренс. Композитные защиты не подвержены коррозии и окислению. Обеспечивают высокое шумопоглощение (для сравнения, при движении по гравийной дороге со стальной защитой возникает "шум пустого ведра", когда камушки стучат по листу металла). Композитные материалы не меняют своих свойств под воздействием влаги и атмосферных перепадов температур.
Композитный материал представляет собой искусственно созданный неоднородный сплошной материал, состоящий из двух или более компонентов с чёткой границей раздела между ними. Компоненты в свою очередь делятся на матрицу (или связующее) и включённые в неё армирующие элементы (или наполнители), которые обеспечивают необходимые механические характеристики материала (прочность, жёсткость и т. д.), а матрица обеспечивает совместную работу армирующих элементов и защиту их от механических повреждений и агрессивной химической среды. По типу наполнителей композиты для автозащит делятся на:
• стеклопластиковые (стеклоткань имеет белые волокна)
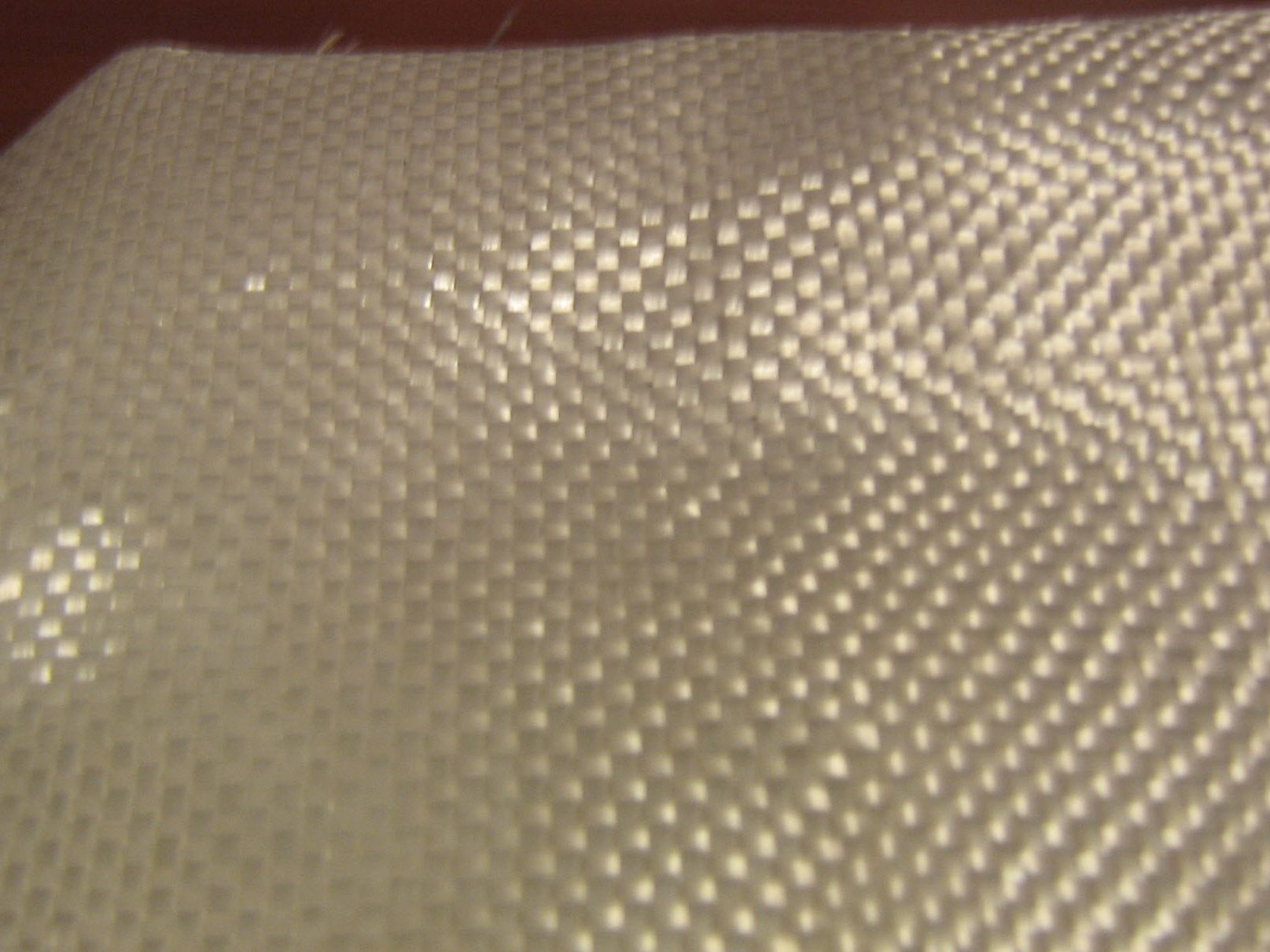
• кевларовые (волокна имеют зеленовато-золотистый цвет)
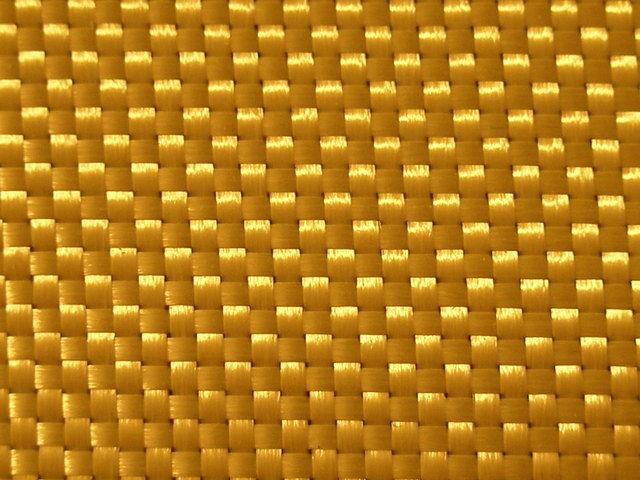
• карбоновые (или углепластиковые) (черные волокна)
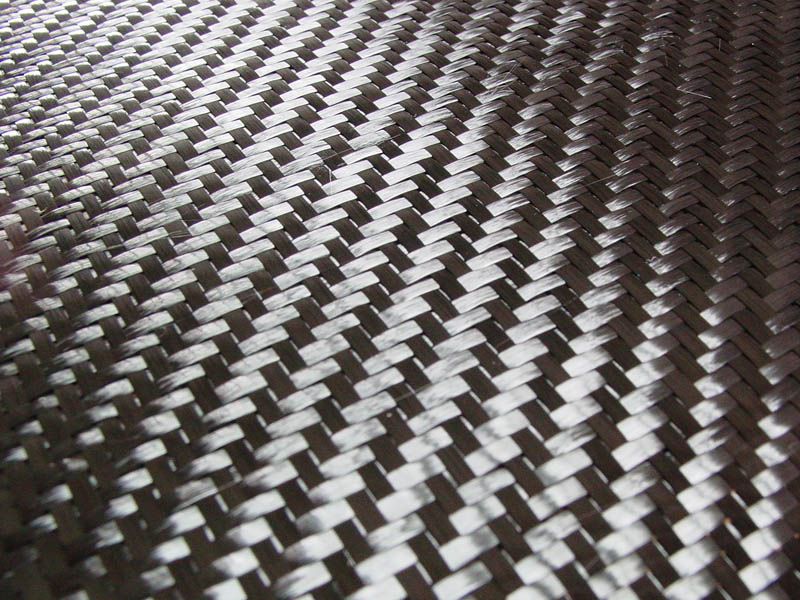
• базальтопластиковые (серые волокна)
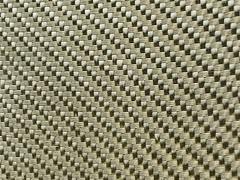
Самые популярные защиты из стеклопластика, прежде всего из-за оптимального соотношения "свойства/стоимость". Здесь качество изделия сильно зависит от вида стекловолокна, который использует производитель. Идеально, когда в качестве армирующего элемента используется стеклоткань, выкладываемая вручную. Но чаще вместо ткани берется ровинг (рубленное стекловолокно), которое вместе со смолой распыляется в форму. При этом частицы ровинга не переплетены друг с другом и связываются только смолой, для достижения нужной прочности приходится увеличивать толщину изделия. Защиты из стеклопластика обладают низкой теплопроводностью, влагостойки, светопроницаемы, устойчивы к механическим ударам и повреждениям, они не ржавеют, не теряют форму и не подвергаются тепловому воздействию.
Защиты из кевлара - самые дорогие. В основе материала - пара-арамидные (полипарафенилен-рефталамид) волокна, очень прочные и легкие. Изначально материал разрабатывался для армирования автомобильных шин, для чего он используется и теперь. Но благодаря своим уникальным свойствам стал широко применятся для изготовления средств индивидуальной защиты, например, защитные вставки в одежду для мотоспорта, антипрокольные стельки и, конечно, бронежилеты. Кевларовый композит прочнее стали в 2,5 раза и лучше стеклопластикового амортизирует ударные нагрузки. Это лучший материал для защит днища автомобиля.
Защиты из карбона (углепластика). Основная составляющая часть углепластика — очень тонкие нити углерода, сломать их очень просто, а вот порвать достаточно трудно. Из этих нитей сплетаются ткани с различным рисунком плетения (ёлочка, рогожа и др.). Для придания ещё большей прочности ткани из нитей углерода кладут слоями, каждый раз меняя угол направления плетения, детали будут жесткими там, где это необходимо, или гибкими — гасить вибрации, если это требуется. Слои скрепляются с помощью эпоксидных смол. Нити углерода получают термической обработкой химических или природных органических волокон, при которой в материале волокна остаются главным образом атомы углерода. Помимо обычных органических волокон (чаще всего вискозных и полиакрилонитрильных), для получения нитей углерода могут быть использованы специальные волокна из фенольных смол, лигнина, каменноугольных и нефтяных пеков. Кроме того, детали из карбона превосходят по прочности детали из стекловолокна, но, при этом, обходятся значительно дороже. Дороговизна карбона вызвана, прежде всего, более сложной, энергоемкой технологией производства и большей стоимостью производных материалов. Например, для проклейки слоев используются более дорогие и качественные смолы, чем при работе со стеклонитью, а для производства деталей требуется более дорогое оборудование (к примеру, такое как автоклав). Карбон не только легкий и прочный, но и очень жесткий материал. В этой жесткости кроется основной недостаток защит картера из углепластика - хрупкость, низкая стойкость по отношению к ударным нагрузкам. Также при производстве углепластиков необходимо очень строго выдерживать технологические параметры, при нарушении которых прочностные свойства изделий резко снижаются.
Защиты из базальтопластика. Этот материал - конкурент стеклопластика. По основным показателям - прочность, жесткость, стойкость к агрессивным средам, теплостойкость - базальтопластики превосходят стеклопластики на основе волокон из простого безщелочного стекла. Базальтовое волокно — материал, получаемый из природных минералов путём их расплавления и последующего преобразования в волокно без использования химических добавок. Базальт, из которого делают волокна, - это органический материал, в природе имеется в неограниченном количестве. Производство пластиков из базальтового волокна - сравнительно новая технология. В 2009 году немецкое инженерное бюро EDAG разработало концепт автомобиля, при производстве которого использовано базальтовое волокно. Как сообщается, «материал отличает лёгкость, прочность и экологичность, к тому же в производстве он обойдётся дешевле алюминия или углепластика».